Sourcing and supplier inspection services matter greatly to avoid daunting scenarios such as materials that do not meet required standards, mismatched labels, and other quality issues resulting in product returns and unsatisfactory customer experiences.
What is Sourcing and Supplier Inspection Service?
Inspecting the quality of products and suppliers involves checking whether the products purchased from or produced by the supplier meet the standards specified in the purchasing contract. The inspection can be carried out by the partner companies themselves or a third-party inspector, especially if you order products from the suppliers abroad. The sourcing and supplier inspection service is expected to have the expertise and experience in building seamless operations, increasing inspection accuracy, as well as improving production process efficiency.
Why Product Inspection Matters?
Product inspection mitigates risks and costs that may be incurred from using defective or subpar products and reduces compensation costs for damages or warranty for products that fail to meet required specifications. Importantly, product inspection ensures that the production process and product quality comply with the laws and regulations of the country in which the products are sold.
Product inspection reduces the risk of having returned or unsold products due to quality issues, which can result in profit loss, additional operational costs, and damage to the brand’s reputation and credibility. On the other hand, if your brand can consistently produce quality products, you gain consumer trust, strengthen brand authority, and support business growth and longevity.
Product inspection must be prioritized, especially for products that are sensitive and prone to contamination, such as:
- Non-ferrous scraps that can be recycled require a thorough inspection to determine metal purity, weight accuracy, contamination risk, and container materials to ensure the product is safe and secure during shipping and complies with the regulations of specific product categories.
- Chemicals that have stringent standards and need to be safely stored to prevent contamination or damage. These products may be at risk of being returned or prohibited from being imported into the destination country. Therefore, the inspection involves ensuring chemical purity and proper management of storage and labels, as well as sustainable practices.
- Starch is a product used as an ingredient in both food and medicine. Product quality inspection is needed to prevent contamination and ensure a smooth and efficient delivery to its destination.
Why do B2B Businesses Need to Give More Priority to Product Inspection?
Product quality inspection is an effective way to provide value to your business in addition to quality products. It benefits businesses in various aspects:
- Mitigates risks before (quality, regulatory, and compliance issues) and after (warranty) the production process to deliver products that meet health and environmental safety standards. By ensuring that production follows regulations and standards according to the laws of each region and at the international level, the inspection helps reduce the number of warranty claims that can negatively affect your company’s reputation and brand image.
- Manages operations costs by ensuring conditions and requirements are followed and met accordingly, avoiding any additional production costs caused by errors.
- Promotes product quality improvement to meet international standards and remain competitive in a global market by ensuring that specific production and quality standards are met and even exceeded.
- Enhances business reputation by ensuring you maintain quality products that meet the needs and expectations of your consumers while reducing the number of returned products or warranty claims after sale.
Product Quality Inspection
Quality inspection for each kind of product uses different standard criteria. Sourcing and supplier inspection services typically use an Acceptable Quality Limit (AQL), which indicates the maximum number of production defects and inconsistencies allowed according to set standards. In the case of food products, the inspection will be carried out according to the WHO Food Code (Codex Alimentarius).
Product quality inspection can be carried out in 3 forms as follows:
1. Screening Inspection
Screening inspection is typically employed for products concerning life safety and valuable properties and usually has a high cost. In electronic device production, for instance, essential parts like capacitors, resistors, and chips need to be thoroughly inspected to ensure functionality and sort out the defective pieces.
2. Lot by Lot Inspection or Sampling
Sampling utilizes less time and cost than screening inspection. It is usually done for products concerning safety and customer satisfaction and involves moderate to high risk. To illustrate, the textile and apparel industry produces large quantities of clothing per lot. Sampling is used to inspect the product quality to ensure that the sewing, fabric, and other relevant components meet the required standards. If products don’t meet the standard, the entire lot will need to be remanufactured.
3. Process Inspection
Process inspection is conducted during production and allows instant fixing, which reduces the amount of damage to the entire production lot. This type of inspection is usually applied to products with moderate risk. For example, automobile production needs careful inspection in each production step, from welding to painting, to ensure that everything in the production process works properly and meets the high production and safety standards.
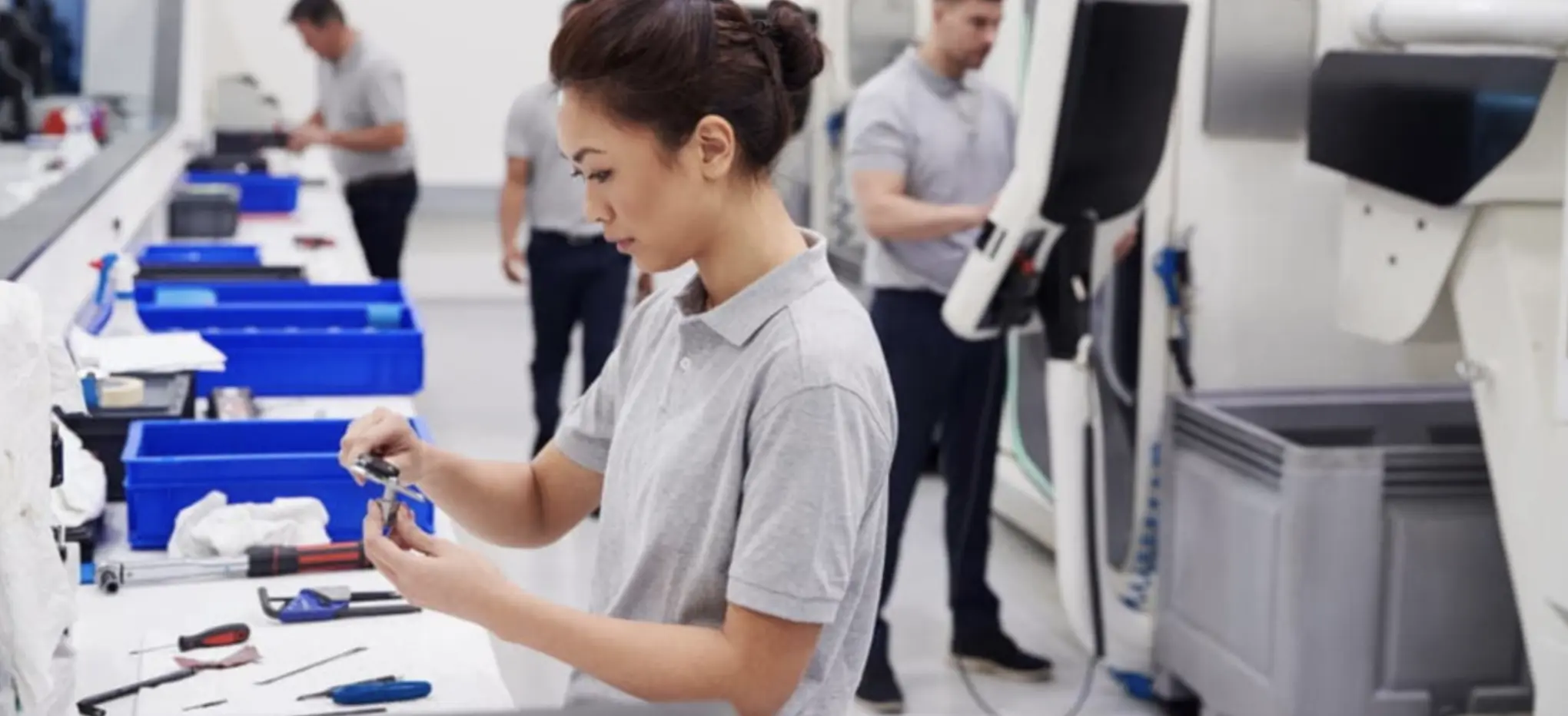
Supplier On-Site Quality Inspection
In addition to inspecting product quality, there are 5 types of supplier on-site quality inspection:
1. Initial Production Check (IPC)
This type of inspection checks whether the raw materials and the material storage meet the standards. The IPC will identify low-quality raw materials and prevent lower-standard-quality products which do not meet customer requirements.
2. During Production Inspection (DUPRO)
This inspection involves checking the product quality when 20-50% of the production is done. The inspection is carried out to determine if the production is in accordance with the agreed conditions, processes, and quality standards. If mistakes are detected, they can be fixed and adjusted to meet required standards, which is more cost-efficient and time-efficient operation-wise.
3. Daily Production Monitoring
This monitoring process aims to check product quality whenever there is a production to ensure the quality and standards are met as specified. This kind of inspection is usually carried out at factories that produce their own products.
4. Pre-Shipment Inspection (PSI)
Pre-shipment inspection randomly inspects products toward the end of the production process, or more than 80% of the production is done. This is done to re-inspect the products to determine that they meet the requirements. It can also check whether the documents comply with the regulations and product standards of the destination country before the products are packed and shipped.
5. Container Loading Check (CLC)
When the production has been completed, the CLC is the final step. This process involves the inspection of packaging, packing, and delivery standards to protect the product from damage during shipping.
Benefits of Using a Sourcing and Supplier Inspection Service
Global sourcing has become the norm, granting businesses access to suppliers from all around the world. Therefore, hiring a third party with a robust local and international network and expertise and experience in product quality audit can significantly benefit your business. Let’s discuss the major benefits of working with a reputable sourcing and supplier inspection service provider:
Product inspection is crucial for businesses using a global sourcing strategy for procuring materials to manage risks and mitigate production defects. This drives customer trust and confidence in your production base.
SCG International is a leading international end-to-end supply chain solution provider with supplier connections in more than 50 countries worldwide that allow us to offer demand sensing and consolidation services, sourcing and supplier inspection services, logistics optimization and warehousing services, and marketing and distribution services. We can cater to the supply needs of industrial, construction, home and living, paper and packaging, and energy applications.
Get in touch for more information about our sourcing and supplier inspection services, HERE